Background of the project:
In the early 1990s, due to the increase in material processing requirements, laser marking, a new technology developed after laser welding, laser heat treatment, laser cutting, laser drilling, and other applied technologies, has become an indispensable processing tool. Laser marking technology has become the most widely used and most mature technology in the field of laser processing with its new contactless, non-polluting and non-abrasive marking process.
The core of Laser Marking Equipment is the laser marking control system. Therefore, the development of laser marking is the development process of the marking control system. In just 7 years, the control system has experienced the large-format era, the rotating mirror era and the galvanometer era in the field of laser marking, and the control mode has also experienced from software direct control to the control of the upper and lower machines to the real-time processing. A series of evolutions that are time-multiplexed.
Project principle:
The laser marking system is mainly composed of Advantech IPC, laser, galvanometer scanning system and f-θ lens. The schematic diagram of the system structure is shown in the figure below:
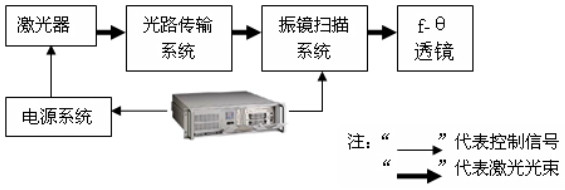
The power system is connected to 220V (50Hz) power supply for IPCs and (gas/solids) lasers respectively. The IPC controls the galvanometer scan system and laser power supply through laser marking software. When preparing for marking work, the IPC sends a signal to the power system to control the laser switch light and its laser power level. At the same time, a certain transformation is made according to the marking coordinate data and transmitted to the galvanic mirror scanning system. The galvo mirror scanning system receives The signal adjusts the X/Y-axis oscillating mirror, that is, the X/Y-axis oscillating mirror is deflected by a certain angle. At this point, the complete optical transmission path is that the beam emitted by the laser is refracted by the X and Y galvanometers, and then is incident on the surface of the workpiece to be marked.
System Features:
Advantech IPC is mainly used to transmit and process laser marking signals in this system, and coordinate the work of each part through the timing function. Due to the timely performance requirements of laser marking, the selection of IPCs is the key. Not only is it required to be able to respond quickly, but it is also characterized by stability, safety, and anti-jamming, so that it can be normally produced under harsh operating conditions. The industrial computer mainly completes the following tasks in the laser marking system:
1. The main switch of the power system is turned on. After the operator has set relevant parameters on the industrial control computer, the industrial computer controls the hardware parts of the system.
2. The IPC extracts the coordinate data of the marking and converts it into an angular deflection signal that can be recognized by the galvanometer system through a certain algorithm.
3. When the marking of a single character is completed, the IPC controls the Q parameter to turn off the laser. At this time, the laser is still in operation. After the entire marking task is completed, the laser power is set to 0, thus completely turning off the laser.
4. The industrial control machine shall carry out timely monitoring and control of the marking process and record and store the information.
Project evaluation:
After the verification of the production of thousands of characters, the high control accuracy has been achieved and the customer's requirements have been accurately completed.
1. High stability: due to the use of a highly reliable Advantech original machine for processing, to enhance the stability of the system;
2. Flexible configuration: It adopts distributed structure and flexible configuration;
3. Cost-effective: Advantech IPC has better scalability, rational use of various methods, and optimizes the cost of the entire system.