Die-cutting and indentation processing is the process of forming the printed matter through the deformation (indentation) and fission (die cutting) of the surface of the printed matter, and is also the key process of the formation of the paper product box. Usually divided into flat die-cut die-cutting indentation, round die-cutting die-cutting indentation and round-pressing die-cutting indentation in three categories, of which flat die-cut die-cutting indentation is the most common. Flat die-cutting die-cutting indentation is based on the structural design drawings of the paper packaging box, and the die-cutting knife line and the indentation steel wire are inlaid on the die-cutting plate of a certain thickness of the wooden plate in order and the indentation steel wire phase. Corresponding bottom molds (or strips) are formed on the die-cutting indenter after being pressed perpendicularly to the substrate, and then stamped into a line for bending and rolling into a certain shape. The most common molding processing method, the quality of its processing directly affects the quality of the paper packaging box. In the following, we will talk about the circumvention of the common defects in flat die-cut die-cutting and indentation processing of paper packaging boxes from three aspects.
Structural design
As we all know, paper packaging boxes are used 250g ~ 350g (used in wine box 250g paper 300g paper or 300g paper 300g paper) board (card) paper printed, usually this type of paper is relatively thick. (See the table below)
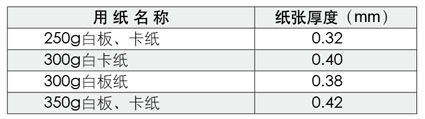
Therefore, in the box design, it is necessary to arrange the evasive relationship between the laps of the associated boxes, that is to say, the box width of the paper box and the sticky mouth should be less than the width of the box corresponding to the box. Thick, it can effectively avoid the defects of the drum head; the width of the box overlapped with the sticky mouth should be less than the width of one box line corresponding to the width of the box after the box is formed, which can effectively avoid the defects of the gap between the edges of the box; In the box-shaped structure, overlap should be adopted as much as possible at the inflection point, which can effectively avoid the defects of the creasing line.
Knife stencil production
Die-cut production is based on the structural drawing of the paper packaging box, after the die-cutting knife wire is bent into a corresponding shape, and is firmly embedded in a certain thickness of the wood board. Therefore, when bending the die-cutting blade line, arc welding should be avoided at the right-angle overlap and the sharp point overlap, which can effectively avoid the defects of poor discharge; the die-cutting knife line that overlaps with the indentation steel wire, Should be spliced to the midline of the indentation steel wire, which can effectively avoid the defects of incomplete cutting and poor discharge; at the arc overlap, the bottom of the arc of the die cutting knife line should pass the midline of the indented steel wire. The utility model can effectively avoid the defects of the explosion angle caused by the extrusion interference of adjacent box surfaces when the carton is formed. For an automatic die-cutting and creasing machine with an automatic stripping function, due to die cutting line, indentation of steel wire lap problems produce poor defects, will seriously affect the work efficiency of die-cutting indentation processing.
Die-cutting and indentation processing
In the implementation of die-cutting and indentation operations, appropriate pressure shall be selected to adhere the indentation line strips or indentation bases, and keep the indentation line grooves or indentations in the groove of the bottom substrate without any foreign matter. It can effectively avoid the defects of the creasing line; strictly control the relative humidity of the work site, can effectively avoid the defects of the creasing line due to the crispness of the dry paper fibers in the environment.
All in all, to ensure the quality of die-cutting and indentation processing, it is necessary to carefully handle every job detail from the beginning of the structural design of the paper packaging box to the end of each step of die-cutting and indentation processing. Only in this way can product quality be effectively guaranteed and operational efficiency can be effectively exerted.