In order to highlight the trademark of the product, rubber shoes are equipped with various decorative materials with a trademark pattern. In the past, molded vulcanized rubber with a trademark pattern was used as a decorative part on plastic parts such as belts. Its features are clear patterns and strong three-dimensional impression, but the disadvantages are the need for vulcanization, and it is necessary to fight hair before sticking on shoes. Brush adhesives (to increase adhesion) not only have many processes, but also have low production efficiency and high cost. In comparison, the use of a trademarked mix as a decorative part eliminates the need for molding, vulcanization, bristling, and brushing of adhesives. The cost is low and the production efficiency is several times higher. Therefore, in recent years, many rubber shoes, especially export-front rubber shoes, have adopted the latter technique.
When over-vulcanized rubber surfaces are overprinted, the quality requirements are high. The common problems in the production are: 1 the pattern is not clear enough, the color is not uniform; 2 the adhesive strength of the pattern material and the rubber is too low, and easy to open; 3 the pattern material has no ductility, when the mixed compound with the pattern is produced When it is stretched, cracks appear in the pattern. In response to these problems, this work has systematically tested the inks used for overprinting trademarks. Now the test is described as follows.
1 experiment
1.1 Major raw materials and equipment
Main raw materials: 1# smoke film, imported; B-type mixed solvent, self-made; 750# coating, Sanmenxia Chemical Auxiliary Factory product; fabric 1# screen printing ink, Yuhang Xingqiao silk screen printing ink plant product; 120# solvent gasoline, 5# Oil, 30# oil and 70# gasoline are all industrial products.
The main equipment: Φ150mm open mill; 120 mesh screen.
1.2 Compound Preparation
Basic formula: 1 # smoke film 100; zinc oxide 60; stearic acid 3 0; reinforcing filler 10 0; softener 2 0-60; sulfur, vulcanization accelerator appropriate amount.
The rubber, which has been weighed according to the formula, is plasticized on an open mill and added with a compounding agent and then evenly sliced. Adjust the amount of sulfur, vulcanization accelerator and softener and other compounding agents to make a variety of mixed film to be dissolved.
1.3 Substrate pressing Substrates used as overprinting marks are special compounds. The rubber, which is weighed according to the formula, is plastic smelted on an open mill, and is added with a compounding agent and uniformly mixed to make flakes; after being parked, it is pressed into a 5 mm thick film on a three-roll calender and then cut into rectangular pieces of appropriate size. Expected to use.
1.4 Performance Test
Adjust the concentration of the paint (or ink) to a moderate level, overprint the brand on the ready-made substrate, and observe the difficulty of the paint (or ink) passing through the screen during wiping and the removal of the screen. Trademark drying speed, color uniformity, and screen reusability.
The overprinted logo is dried and placed in a vulcanization tank for vulcanization. The vulcanization condition was 134°C x 40 min. Observe the color of the overprinted logo, change the logo pattern when testing the stretched film, and the adhesion of the pattern to the substrate.
2 Results and Discussion
2.1 Selection of Ink Material
Four inks are formulated with different host materials. 1# ink is formulated with 750# coating as the main material; 2# ink is prepared with fabric 1# screen printing ink as the main material (applicable substrates are mostly canvas and artificial leather); 3# ink is blended with natural rubber latex. The pigment paste; 4 # ink is made of NR as the main material of gasoline glue. The overprint trademark test was conducted on the substrate by wire mesh. The results are shown in Table 1.
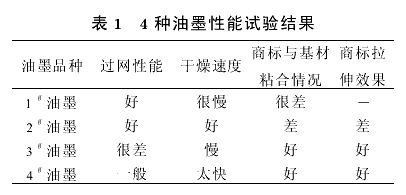
It can be seen from Table 1 that 1# and 2# inks cannot be used because the main material of 1# ink is polar material of water solvent, and the main material of 2# ink is also polar material, and they are with non-polar NR. The bonding effect is worse. In addition, 2# ink also has the disadvantage that the trademark pattern is cracked as the substrate is stretched.
Poor network performance of 3# ink is caused by the easy skinning of latex, especially when the scraper wipes on the screen, it quickly clumps, not only clogging the mesh, but also difficult to clean, the process is not easy to solve, so despite It combines well with the substrate and cannot be used.
4# ink is easy to pass through the net when the concentration is small, and the scrape is also united when the scrape is scraped back and forth, but the clumping speed is slow, and after the netting is blocked, soaking with a high-grade solvent oil can dissolve the filament mass, and the filament mass also dissolves. Easy to clean. Taking into account that by adjusting the solvent evaporation rate is expected to change this unfavorable factor, determine the NR as the main material of 4 # ink for the next test object.
(to be continued)