In recent years, the competition in the steel industry has become increasingly fierce, and companies can only achieve further development if they continue to carry out technological transformations, improve product quality, and reduce production costs. In order to meet the needs of the market, Xuangang has built two six-machine six-flow continuous casting machines with the same model, and in the subsequent upgrades, the continuous expansion of the continuous casting machine has been carried out. At present, the annual production capacity of the single machine has exceeded one million. Ton. This paper mainly introduces the network structure, bus layout and main functions of the automation system after the transformation of two continuous casting machines.
Overview
The 4# and 5# continuous casting machines of Xuanhua Steelmaking Plant are key projects of Xuanhua Iron and Steel Co., Ltd., and their automation control level has reached the domestic advanced level. The system adopts the popular three-integrated design and uses fieldbus technology and automation system. The software and hardware are mainly based on Rockwell Automation's products, which constitute a three-level network structure, which realizes automatic control of production and production scheduling control and product quality control of continuous casting machine.
The system network structure is shown in Figure 1:
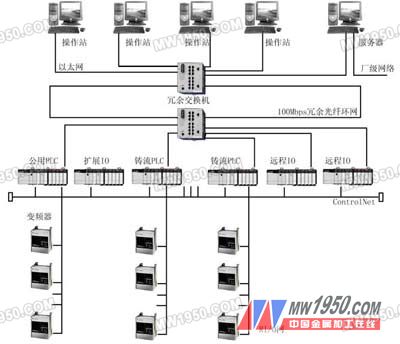
Figure 1 Control system network structure
As can be seen from the above figure, the automation system of the continuous casting machine takes into account the needs of practical applications, makes full use of the resource characteristics of hardware and software, and builds a three-layer network structure, namely the information layer, the control layer, and the device layer.
Information layer
The information layer shall provide network interface for operation, maintenance and plant-level computer system of the continuous casting machine body, access workshop-level production and management data, provide services for data collection and monitoring of the entire plant-wide control system, and accept production scheduling instructions. Coordinate the production of the whole plant. This layer is characterized by a large amount of data, but has no excessive requirements for real-time performance. At the same time, in order to facilitate the interconnection of PLCs and computer systems of different manufacturers, necessary control and coordination are performed, and thus a TCP/IP protocol conforming to public standards is adopted. 100Mbps rate Ethernet.
Considering the reliability requirements of industrial control and the harsh environment of industrial sites, Ethernet is composed of redundant optical ring networks, and two industrial Ethernet switches have redundant management functions. One server and four operation stations of the continuous casting machine are connected to the network through an Ethernet card. Each frame of the PLC system in which the CPU module is installed is accessed through the Ethernet interface module.
2. Control layer
The control layer is responsible for the transfer, exchange and coordination of control data between the common PLC system, each cast PLC system and the remote FlexI/O, and provides functions such as network programming, program maintenance, device configuration, and troubleshooting.
This layer of network not only requires a stable and reliable connection, but also ensures the real-time delivery of information. ControlNet uses a bus topology with a communication rate of 5 Mbps. Its characteristic is that ControlNet is deterministic, which means that I/O devices and controllers on the network communicate at predetermined times. Every component in ControlNet has been pre-determined for communication time and duration, so it is very stable and reliable, especially for industrial applications with high time requirements. At the same time, to ensure that communication is not interrupted, at this level we use redundant communication media to further improve reliability.
3. Equipment layer
The equipment layer is mainly used to connect the main line transmission equipment, that is, the inverter and the soft starter, directly to the PLC system, and no longer realize the control through the traditional digital and analog connection. This is not only convenient but also fast, and can also be collected. Field device data, configuration, monitoring and real-time control. This layer uses the RemoteIO network.
The three-layer network structure makes it possible to select the appropriate communication method according to the specific application requirements of the continuous casting machine system. This network architecture not only provides EtherNet/IP, ControlNet, and RemoteIO network connections, but also includes advanced software interfaces optimized for automatic control. To ensure efficient data transfer.
Next page