System composition and function
1. Hardware configuration
Each continuous casting machine automation system hardware consists of 9 sets of Rockwell Automation's ControlLogix series PLC, 4 operating stations, 1 server and remote FlexI/O station. The main production line equipment in the transmission system is driven by vector inverters. Soft starter, auxiliary drive equipment is controlled by MCC. The instrument system is mainly composed of molten steel rapid and continuous temperature measuring system, large bag, medium-weighing weighing system, crystallizer liquid level monitoring and regulating system, crystallizer water, two cold water flow detection and regulation system.
The common system of continuous casting machine adopts a PLC system with extended frame, which is used for the detection and control of the common equipment on the main body of the continuous casting machine and the blank part. The PLC system is used for the monitoring of the casting system. ,control. The operation station is arranged in the main control room and the cutting operation room for monitoring, operating, processing alarm information and necessary human intervention for the continuous casting machine equipment. The server is used to collect production data and process, save, and transfer it.
2. System function
The continuous casting machine automation system adopts three-electricity integrated design. All electronic control and instrument control signals are connected to PLC. The thermal resistance, transmitter, flowmeter and other measuring instruments installed in the field collect instrument data, switches, limit, etc. The equipment collects the process production process data and equipment operation status, all data is transferred to the PLC system, and combined with the instructions from the upper operation station, the process loop adjustment, the electrical equipment sequence control and the transmission equipment control are implemented according to a preset program.
1) Instrumentation system
Instrumentation detection mainly includes rapid and continuous measurement of large and medium-sized steel water temperature, large and medium-sized steel water weight measurement, mold water pressure, flow rate, inlet and outlet temperature difference measurement, secondary cooling water pressure, flow measurement and adjustment of each section. In order to reduce the labor intensity of the operator and improve the quality of the billet, the continuous casting machine also collects the liquid level of the mold steel, and adjusts the opening degree of the plug in the electric cylinder to keep the molten steel level stable.
The secondary cooling water distribution system has manual and automatic control functions, including water distribution, water meter setting, tracking adjustment, water distribution correction adjustment, water flow, pressure, temperature and valve position display. The PLC realizes on-site data acquisition, tracking adjustment, and the operation station completes the setting of the water meter, the display of water flow, and the data recording, data printing and statistics functions.
Manual and automatic control: four stages of water distribution per flow, namely the foot roller section, one section, two sections and three sections, each of which has a manual/automatic conversion function. In the manual mode, the staff can directly change the valve opening degree by setting the valve opening degree on the operation station screen; in the automatic mode, the system will automatically adjust the water volume according to the speed of the drawing speed according to the preselected water meter. During the casting process, The amount of water supplied can be corrected at any time according to the temperature of the billet. The second cold water regulation flow chart is shown in Figure 2.
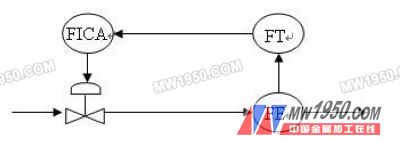
Figure 2 Second cold water regulation flow chart
Selection and modification of water meter: Several dozen water distribution parameters are available for use in the operation station. The parameters include: number, steel type, section and water distribution ratio of each section. The operator can modify the parameters to change the water distribution at any time.
2) Electrical system
The detection and control of electrical equipment mainly include: rotation of the big bag turret, arm lifting, large bag opening and closing, tundish walking, centering, lifting, crystallizer vibration, vibration frequency adjustment, tension leveling machine transmission, tension correction Under rolling, the spindle is lifted, recovered and tracked, stripped and stored, and the billet is cut to length, and the roller path before and after cutting, the conveyor roller, the steel turning machine, the casting blank separator, and the stepping cooling bed are controlled. The detection and control of hydraulic system, oil and gas lubrication system and dry oil lubrication system are also completed by PLC.
All the main production line transmission equipments are driven by frequency converters. The continuous casting machine uses more than 100 frequency converters from the ladle turret to the horizontally moving steel and other mechanical equipment. The power range is from 0.75KW to 45KW. All inverters are connected to the RemoteI/O communication adapter through their built-in communication interface, and are directly connected to the nine RemoteI/O networks formed by nine RIO interface modules to form a transmission system based on the Remote I/O network. Considering the connection distance of the Remote I/O network and the real-time requirements of the system, the communication rate of 115.2Kbps is adopted.
The RemoteI/O network works in the scanner mode, and the PLC processor establishes a serial communication link through the RIO interface module and the remote I/O adapter. The communication interface of the inverter provides a direct and digital communication link for the network equipment in the RemoteI/O network. The system establishes the input and output data links by configuring the I/O tags of the PLC and using the communication interface. For PLC, each inverter is regarded as a remote frame with I/O modules installed. Only need to read and write these modules, you can send commands to the inverter connected to it to control the operation of the equipment; The data can be read from the inverter, the operating status of the device can be monitored, and the data can be transferred to the PLC in real time. Through the screen, the operator can provide real-time and detailed information on the operation station display of the main control room, and can directly operate the equipment. Even when the inverter issues an alarm, when the fault occurs, the inverter can be reset in time to avoid the cause. The accident was not handled in time. The electrical system of the continuous casting machine realizes the real-time remote network control of the transmission equipment, enabling the PLC to realize the networked digital control of the drive of the frequency converter, replacing a large number of hard wirings with a communication cable, and the traditional analog quantity and switching quantity. Compared with the control method, not only the real-time, accuracy and reliability of the system are greatly improved, but also the cost of installation, debugging and maintenance is correspondingly reduced.
3) Operator station
HMI screen software according to the process requirements, with main screen, cast flow profile, blanking area overview, tension leveler and spindle, crystallizer level, crystallizer vibration, large bag / medium package weighing, hydraulic system, drive Nearly 20 pictures of device operation status and PLC status. Through the monitoring of the HMI, the operator can observe the running status of the equipment in real time, modify the process parameters according to the authority, and timely handle the alarm events. If necessary, the equipment can be manually interfered with.
4) Command and dispatch system
Steelmaking is a complicated production process. The quality of continuous casting billet is directly affected by casting conditions and process conditions. Even if advanced technology, equipment and technology are adopted, due to the influence of continuous casting production process, furnace transfer and equipment failure And the unstable operation will inevitably cause fluctuations and abnormalities in the production process, so that the quality of the slab is damaged to varying degrees, and the impact on the subsequent rolling process and the quality of the final product cannot be ignored, resulting in economic and product reputation for the enterprise. Loss. The continuous casting machine needs to know the situation of the previous process in time. The converter and refining system must also master the casting condition of the continuous casting machine. In order to facilitate the intuitive and quick understanding of the whole process of production, the automation system of the continuous casting machine provides network excuses, converters and refining. The systems such as the argon blowing station are connected to the plant-level management network to provide data for the unified coordination of production scheduling.
Application effect
The automatic control system of continuous casting machine of Xuanhua Steelmaking Plant integrates PLC control technology, screen monitoring technology, network communication technology and frequency conversion speed regulation technology. The design of three electric integration adapts to the development trend of automation and realizes the foundation of continuous casting machine. The automatic control of the production process completes the automatic interlock control of the continuous casting production field equipment, the detection and adjustment of the medium parameters, the data communication processing, the fault alarm diagnosis and the online monitoring of the production status. After more than three years of operation verification, the system control function is advanced, stable and reliable, effectively improving labor productivity, reducing the labor intensity of the staff, and has played an active role in smooth production, production, increased production efficiency and maintenance of safe production. effect.
Previous page