(B) Imprinting process
(1) Cut-off Cuts wide-width material into a narrow width of material of the desired width. The width is at least 20mm wider than the finished product. The slitting of a narrow web requires a neat end face with proper curling tension.
(2) Molding Compared with other printing methods, the printing equipment used for holographic marking printing does not require an inking device, but instead completes the printing process by a stamping device on a metal stencil on the embossing machine. Imprinting is performed according to the heat, cooling, and peeling processes. Embossing transfers the interference fringes on the stencil to the printing material.
Moulding replication leveling pressure and rolling two basic processing methods. For different imprinting methods, different special equipments must be provided.
Flat Press Flat Press is an intermittent printing process where the entire hologram platen surface is pressed simultaneously. The flattening and multiple embossing machine is as shown in Fig. 1. It is composed of a feeding cylinder, a tensioning wheel, a sprocket wheel, a take-up wheel, a take-up roller, a metal platen, a hot press die, and a cold press die. Each imprinting process can be divided into several stages: sheet feeding, pressurizing, holding, stripping, and retracting. The entire process takes several seconds.
The flat pressing process has a high requirement for the metal stencil. If the stencil thickness is not uniform, high-quality hologram marks cannot be obtained no matter how much the pressure is increased. Although the flat pressing process has a low production efficiency, as long as the holographic stencil quality is high, high-quality holographic markings can still be obtained.
Rolling Rolling is divided into two types: round press and round press. Among them, the round-flattening type is still an intermittent production method, and the efficiency is not high, but it is possible to manufacture a molded hologram mark with a large area. The round press type is a continuous production method, which not only has high production efficiency, but also can produce a large area of holographic signs, which is mainly used in mass production occasions. Round press-type imprinting machine is composed of thermostat heating platform, moving lithographic plate, holographic nickel stamper, pressure roller and film wheel. Each imprinting process can be divided into several steps: sheet feeding, rolling cooling, and peeling.
Round pressure circle is currently the most advanced way, as shown in Figure 2. The characteristics of this production method are:
1 Pressurization maintains a busbar contact between two press rolls, so the applied pressure is small and the holographic plate has a long service life.
2 Because the pressure is small, the pressure roller can be longer and larger in diameter (for example, 66cm in length and 10cm in diameter or larger), and a large-scale molded hologram mark with a width of more than 30cm can be manufactured.
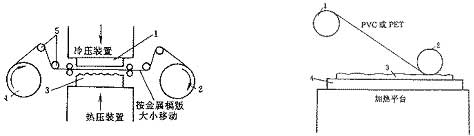
Fig.1 Flat Press Stamper Fig.2 Circular Press Stamper
1- Metal platen 2 - Take-up roller 3 - Holographic plate 1 - Suck wheel 2 - Roller 3 - Metal plate 4 - Mobile tablet
4-feed roller 5- tensioner
3 Rolling speed is very fast, and some have reached 1524cm/min, which can achieve high production efficiency.
The DC-3 precision molding press manufactured by Glogal Images Inc. of the US can process both PVC and PET. The speed can reach 20m/min and the maximum hologram can reach 30cm. There are also many domestic manufacturers of holographic presses.
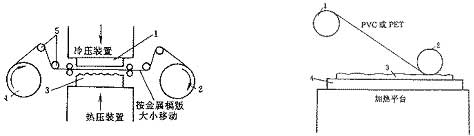
Figure 3 round press
1-Feeder Roller 2 - Embossing Roller 3 - Receiving Roller 4 - Cooling Roller 5 - Plate Roller 6 - Heater
(to be continued)